Helping businesses dramatically improve their product and manufacturing performance!!!
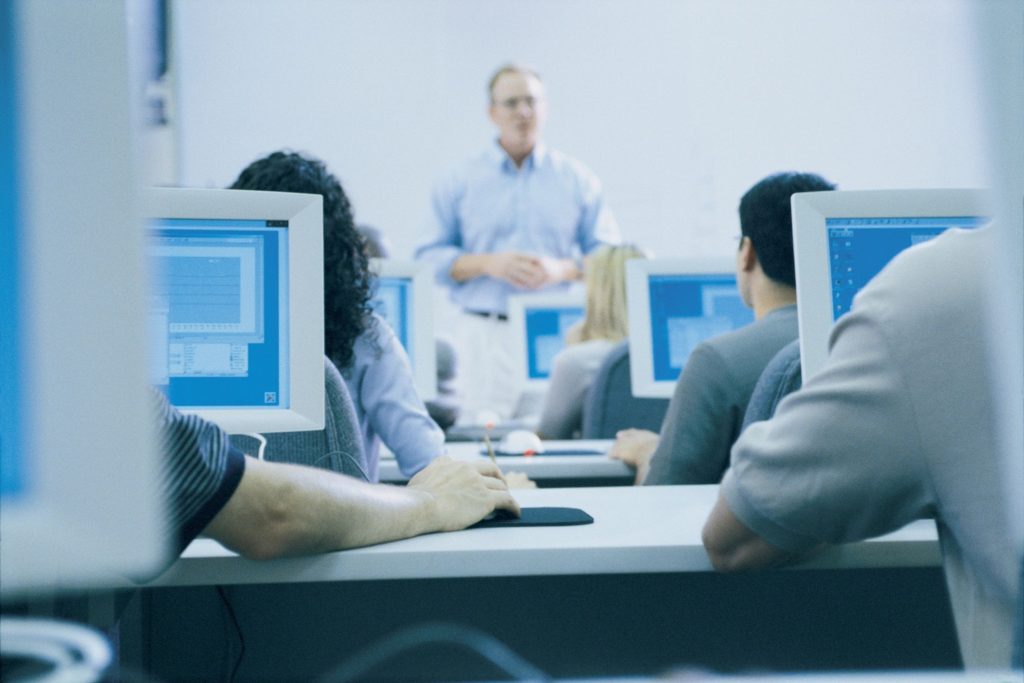
The instructor teaches for both UCI and UCSD though their Extension and Corporate Training Programs.
Students will learn basic and advanced statistical methods plus strategies that will significantly increase their ability to take product and process performance to the next levels. These statistical tools provide the means to perform comprehensive root-cause-analysis to eliminate those difficult to resolve problems. Additionally, these statistical methods taught provide the foundation of the highly touted Six Sigma Methodology.
Statistics provides managers, scientists and engineers the opportunity to make objective data based decisions regarding the selection of option “A” or “B” or “C” to resolve product and process performance challenges. Statistical methodology provides an effective and efficient means to help you understand cause-and-effect relationships between product or process design inputs and outputs. Additionally, utilizing these statistical tools during the product and process development phases will result in superior product and process performance that will be both stable and predictable. Also, students will learn several statistical tools to sustain process performance during the production phase.
Topics Covered: | Usage: Provides knowledge for superior results | ||
- Descriptive Statistics
|
Use for initial data screening to estimate: Mean, Standard Deviation, Outliers, Trends, Patterns, Sources of Variability, Distribution Fitting, etc. | ||
- Inference Statistics (Hypothesis Testing & C.I.s)
|
- Use to compare a single sample Mean or Standard Deviation to a target. - Use to compare 2 samples Means or Standard Deviations to each other.
|
||
- Analysis of Variance (ANOVA)
|
Use to compare 3 or more sample Means when there is one or more input Factor(s). | ||
- Regression Analysis
|
Use to build a prediction model to correlate the input (factor) to the output (response) for either linear or curvilinear relationships. | ||
- Gage Repeatability & Reproducibility (GR&R) Study
|
Use to quantify the capability of the operators and the measurement system. | ||
- Statistical Process Control (SPC)
|
- Use for process monitoring of either variable or attribute data. Control Charts indicate when a special cause effect is influencing the process output and signals the need to re-center the process. Also used to indicate the process is stable. - Use a Process Capability Study to establish process control limits & estimate process capability - Use Process Capability Indices to estimate the short and long term process yield |
||
- Acceptance Sampling
|
Use Acceptance Sampling Plans to efficiently inspect both incoming raw materials and outgoing products. | ||
- Multi-Vari Analysis | Use to identify and quantify high sources of variation in both product and process performance that should be alleviated. | ||
- Design of Experiments (DOE) Introduction | DOE is the most powerful product and process performance optimization tool. Use to identify the optimal settings of the most significant product and process inputs while simultaneously reducing the amount of variation in both product and process performance. |
Who Should Attend:
This course is intended for Quality Managers, Quality Engineers, R&D personnel, Product Engineers, Process & MFG Engineers, Designers, and Six Sigma Green & Black Belts.
Location:
- In-house training at your facility is the most cost effective approach for training. Additionally, some time can be used to discuss your specific product or process improvement opportunities and how to best utilize the various statistical tools.
- Public training is scheduled based on interest.
Statistical Consulting:
- Three free consulting hours included with on-site corporate training, good for 60 days after training is completed.
- Additional consulting is available upon request
Course Materials:
Participants will receive a course manual and a Demo CD of the software used during training, which is active for 30 days after it is loaded.